Eco-Cut has a thick tool diameter with abundant rigidity and grooves with excellent chip discharge, which has the advantage of being less likely to cause problems in turning.
In particular, in minor diameter machining, conventional products such as boring bars have low tool rigidity, making it difficult to process with high efficiency.
In addition, the space for discharging chips is small, and problems related to chip disposal are likely to occur.
▽ A major advantage of tool consolidation and a significant reduction in machining time
1) Tool aggregation: Conventional 4 tools can be used in 1 tool
↓ When machining parts with such a shape
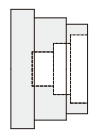
so far | EcoCut Can be processed with only one stick |
result |
![]() |
B minor diameter Turning C End face turning D External Turning * Reverse rotation of the workpiece |
- Simplification of programs ・Decrease in the number of items in stock ・Significant cost reduction due to tool consolidation ・Reduction of tool setup time and accuracy time |
2) Flattening of hole bottom
EcoCut | Normal Indexable Drills |
![]() The bottom of the hole is finished flat. |
3) First in the industry! Equipped with back coolant! (According to our research)
EcoCut can supply internal coolant.
In addition, the 2.25D body has a back coolant function, which greatly improves chip discharge.

B Helical groove (high rigidity)
C End face restraint (2.25D body only)
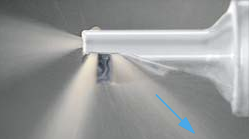
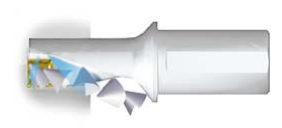
4) DENSIMET (tungsten alloy) is used for the body of 3.0D.
The high modulus of elasticity and specific gravity improve vibration absorption during machining, contributing to high-precision machining, excellent surface quality and extended tool tool life .
body | material | Modulus of elasticity | specific gravity |
1.5D、2.25D | steel | 210,000N/㎟ | 7.85 |
3.0D | DENSIMET | 360,000N/㎟ | 17.50 |
Anti-vibration action | The amount of deflection is 40% less than steel |
![]() |
![]() |
(FAQID:43)