With Eco-Cut, you can perform processing work on flat surfaces, such as counterboring machining, with a single unit.
▼ References
minor diameter High-efficiency machining
Example) When starting Pilot hole φ16 to minor diameter machining, the boring bar usually uses φ12, but EcoCut can use φ16.
The tool rigidity is high and it is equipped with a groove for chip discharge, so it realizes high-efficiency and stable machining.
EcoCut | Bowling Bar | |
Tool stiffness and chip evacuation |
・High tool rigidity ・Chips are discharged from grooves in the body. ![]() ![]() ![]() A Tool diameter φ16 B Pilot hole diameter φ16 |
・Low tool rigidity and vibration ・ Chips are discharged from the clearance gap of the body and holes. Prone to chip jamming ![]() ![]() ![]() C Tool diameter φ12 D Pilot hole diameter φ16 |
Machined surface
|
![]() E Near the bottom of the hole Good processing surface and chip discharge! |
![]() F Near the bottom of the hole G Vibration caused during processing Near the bottom of the hole, chips cannot be discharged. Scratches appear on the machined surface |
EcoCut vs Conventional Processing
Tool aggregation by EcoCut eliminates the need for frequent workpiece reversal and tool changes.
In addition, EcoCut's biggest advantage is the high efficiency of minor diameter turning, which significantly reduces machining time.
EcoCut | Conventional processing |
minor diameter ・End face Outer diameter and end face Drilling Bottom Flat ![]() |
![]() H Outer diameter and end face I minor diameter ・End face J Bottom Flat K Drilling |
Machining time
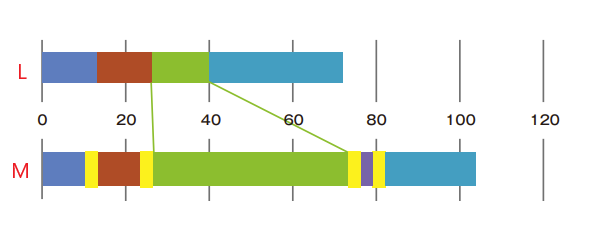
L EcoCut
M Conventional processing






Tool diameter | Cutting speed Vc | Feed amount f | Infeed AP | |
EcoCut | φ16 | 160m/min | 0.15mm/rev | 2.5mm |
Conventional processing | φ12 | 160m/min | 0.1mm/rev | 1.0mm |
(FAQID:37)