What kind of tool is a thread mill? We will introduce you from the basics to how to use it. Thread mills are an ideal solution to deal with threading problems. Through this article, it is possible to expand the range of thread machining in your machining center by using a thread mill.
table of contents
- At first
- What is a thread mill?
-
How to use the thread mill
- Advantages of Thread Mills
- Disadvantages of thread mills
-
frequently asked questions
- Machining of conventional JIS2 grade screws
- I want to pass with a screw gauge. What is the procedure for adjusting the tool diameter correction value?
- Thread processing of high-hardness steel of about 60HRC
- Over-size threading
- Tapered threading shorter than short threads
- Machining of insert screws
- I want to make sure that I don't hit the bottom of the pilot hole.
- Machining the left thread
At first
In this article, we will introduce a method of machining threads using a thread mill that is effective in cases where it is difficult to solve the problem with tapping alone, such as when the machine stops due to a large load during machining, or when there is no tap of the specified oversize.
Thread mills are an ideal solution to deal with threading problems. Through this article, it is possible to expand the range of thread processing at your machining center by using a thread mill.
What is a thread mill?
2.1 How does the thread mill work?
A thread mill is one of the tools that performs "threading" machining. In the pilot hole drilled in advance, the tool (= thread mill) moves with a spiral movement while rotating, and the screw is cut. Machines such as machining centers that perform this movement require a helical interpolation function (and simultaneous three-axis control).
![]() |
![]() |
|
|
Some thread mills perform pilot hole drilling and threading at the same time. Example: AT-2 Series
2.2 Types of Thread Mills
There are two types of thread mills: a solid type in which the entire tool is made of carbide or high-speed mills, and an indexable type in which inserts (inserts) are replaced.
Solid Type
There is a wide range of sizes from small diameters, and the number of blades is large and efficient.
Solid Type - General Purpose Type
The pilot hole is machined in advance, and the pilot hole is threaded. There is no bite part like a tap, and the effective thread length can be secured for a limited pilot hole depth. Can be resharpened.
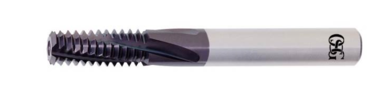
Solid Type - Type with Bottom Blade
Pilot hole machining and thread machining can be processed at the same time. There are series that can process screws of high-hardness steels up to 60HRC and series for high-efficiency machining of non-ferrous metals.

* Some series and sizes of solid types cannot be resharpened.
Indexable Type
The high holder rigidity is advantageous when machining large thread sizes and large pitches. Inserts can also be replaced to accommodate other thread types and sizes. Indexable type holders are available in multi-point and single-point versions.
Indexable Type - Multipoint
Inserts with multiple threads can process several threads at once, so they can be processed in a short time.
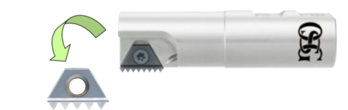
Indexable Type - Single Point
Since the triangular inserts are processed one by one, processing can be done with less load. Therefore, it is advantageous for machining with long thread lengths and protrusions and machining with large pitches.
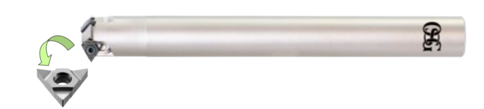
Recommended lineup of solid type thread mills
-
AT-1 One Revolution Thread Mill
By preventing it from collapsing, conventional two-pass machining can now be processed in one pass!
-
AT-2 Thread Mill with Bottom Blade for High Hardness Steel
Simultaneous processing of high-difficulty high-hardness steel processing by helical drilling + threading!
-
AT-2 R-SPEC High Efficiency Thread Mill with Bottom Blade for Non-Ferrous Metal
Dramatically reduce machining time and prevent misalignment of machining positions in casting holes! Also for high-performance resin processing!
3: How to use the thread mill
3.1 Pilot Hole Drilling
3.2 Selection of thread mill
As a guideline for selecting a tool for a thread mill, it is necessary to check whether the following are met for the screw to be machined.
- Is the pitch of the screw correct?
- Is the blade length (neck length) sufficient (blade length (neck length) - about 2 pitches as a guide)
- Is it compatible with the material you want to process?
If you use OSG's ThreadPro program creation app for thread mills, you can enter the information of the screw you want to machine and display the tools that can be machined dimensionally. Therefore, it is easy to select a tool that satisfies "1" and "2".
・ ThreadPro, a program creation application for thread mills,
After selecting a tool in ThreadPro, you can check with a message if it is not supported on the screen for selecting the material to be machined.
You can check the compatibility of each thread mill with the material in the catalogue or refer to the OSG product search.
・ Click here for the thread mill catalog
* In the case of parallel screws such as metric screws and unified screws, the shape of the internal thread and the screw are different, so the tool (insert) cannot be shared. The pipe screws can be shared with external and internal threads.
3.3 Preparation of the machining program of the thread mill
If you're new to ThreadPro, here's a video on how to use ThreadPro to create machining programs.
3.4 Preparing a Gauge That Can Inspect the Thread Accuracy of Drawing Instructions
This is a gauge inspection to check whether the machined screw meets the thread accuracy of the drawing instructions. You can check the gauge selection method from the following.
3.5 Adjusting the Thread Milling Process When the Gauge Does Not Pass
Since the thread mill is a cantilevered tool, it may not pass inspection with a thread gauge due to vibration or deflection during machining. At that time, the thread mill must make adjustments by machining movements. If you select "Cutting Edge Reference" when creating a program with ThreadPro, a program creation app for thread mills, you can make adjustments to pass the inspection with the screw gauge without changing the program by simply changing the value of the tool diameter correction. In addition, at that time, RPRG, which is the tool radius correction value (reference value) that aims to pass the thread gauge of the selected thread accuracy, is displayed. By using this, you can aim to pass the gauge with a small amount of adjustment. If the gauge still does not pass, adjust the tool diameter correction value in increments of 0.02~0.03 and check whether it passes the screw gauge inspection.
* For the solid type (for internal threads), the RPRG when machining the minimum machining diameter (thread accuracy 5H) is displayed on the actual product. If you want to machine a thread size larger than the minimum machining diameter or other thread accuracy, enter the RPRG value displayed in Thread Pro in the diameter correction area.
When looking for a tool diameter correction value that the gauge accepts, be careful not to remove the workpiece from the machine. This is because once the workpiece is removed, the position will shift and the result of adjusting the tool diameter correction will not be able to be judged correctly.
In the case of internal threads
- If the plug gauge on the street side stops (if the finish of the internal thread is small), the tool diameter correction value displayed in ThreadPro can be adjusted to a larger screw because the trajectory of the tool arc moves larger.
- If the plug gauge on the stop side passes through (when the finish of the internal thread is large), the trajectory of the arc of the tool moves slightly by increasing the tool diameter correction value, so it can be adjusted to a smaller screw.
In the case of external threads
- If the ring gauge on the street side stops (if the finish of the external thread is large), you can adjust the thread to a smaller screw to move the arc trajectory of the tool by reducing the tool diameter correction value displayed in ThreadPro.
- If the ring gauge on the stop side passes through (when the finish of the external thread is small), the trajectory of the arc of the tool will move greatly by increasing the tool diameter correction value, so it can be adjusted to a larger screw.
4: Advantages of Thread Mill
4.1 Other thread sizes and thread accuracy can be processed with one screw
The number of taps is required for each thread size and thread accuracy, but the thread mill can process right and left threads with the same tool by adjusting the movement (path) of the tool, and can also handle screws of other sizes with the same pitch. In addition, by fine-tuning the movement of the tool, it is possible to target a single thread mill for screws equivalent to 1st, 2nd, and 3rd grade, insert screws for inserting screw inserts (coils), and specified oversizes according to the thickness of the plating film.
4.2 Can be processed with low load
When machining large-sized screws, the spindle rotation may stop during machining due to insufficient spindle torque of the machine. This is a specification that stops the program operation for safety when the processing machine detects a torque above a certain level. For each machine, the materials that can be threaded and the approximate size of the screws are described in the specifications. In order to process without stopping the machine, it is necessary to process with a small amount of torque, which may not be coped with by the type of tap alone.
The thread mill processes the inner side of the pilot hole, so it can be processed with a lower torque than tap processing. Therefore, even thread machining of large sizes and high loads that would stop on a small machining center can be processed with a thread mill, so it is possible to expand the range of support with your machine.
4.3 Easy to discharge chips
Especially in the case of machining with spiral taps, chips generated by machining are discharged to the outside through the narrow grooves of the pilot holes and taps. If the discharge of chips is delayed, it will be broken in no time due to chip chewing or blockage. On the other hand, chips generated by thread mills do not connect, and the shape is compact and easy to discharge. In addition, the clearance between the pilot hole and the tool is wide, making it possible to smoothly discharge chips and make it easy to aim for stable machining.
4.4 Suppression of the occurrence of stop marks in tapered threading for pipes
In the tapping process of tapered threads for pipes, a trace of processing called a stop mark is left after processing. Depending on the degree, this stop mark can cause gas or liquid to leak out of the pipe connected by the screw. In tapered thread processing with a thread mill, it is processed by intermittent cutting to separate chips into small pieces, so it can be processed without this stop mark. In addition, the machining load tends to be high because the tap is cut even in a fully threaded part, but the thread mill can be processed with a lower load than that, so instability due to high load can be suppressed, and a stable shape with good roundness can be achieved.
4.5 Advantageous for screwing of stop holes with no pilot hole margin
The thread mill does not have a part that corresponds to the bite part of the tap (* Except for some parts. AT-2 series, etc.) can be processed with almost no defective threads. Therefore, it is effective when you want to ensure the effective thread length as long as possible in a stop hole where the pilot hole depth is limited. If a flat drill is used during pilot hole machining, a longer effective thread length can be obtained at the stop hole in combination with a thread mill.
5: Disadvantages of thread mills
5.1 Longer processing time compared to taps
Thread machining in thread mills tends to take longer than taps. In contrast to the linear movement of the tap process while turning forward and reversing, the thread mill performs the following movements.
In the internal thread machining program (created by ThreadPro) with the thread mill as the R point, the center of the mouth of the pilot hole is used as the R point and the following movements are used. Depending on the processing content, it may be processed multiple times in the radial or axial direction.
・Move to a predetermined depth from a position of Z+5mm from the center of the mouth of the pilot hole
・ Approach with fast forward while leaving clearance
・Approach (cutting while helical cutting)
・Main cutting (360° helical cutting)
・ Release (detachment while helical movement)
- Fast forward back to the center
In addition, depending on the length of the thread and the processing content, the thread may be processed multiple times in the radial direction to complete the screw, and the machining time tends to be longer. In recent thread mills, it has become possible to complete screws under high-efficiency conditions and with a small number of times due to specifications that distribute the machining load and increase tool rigidity, and the machining time is approaching that of tap machining.
5.2 Requires an in-depth program
The machining of a thread mill requires detailed coordinate calculations because the movement of the arc and the axial movement are combined, and the accuracy of the screw is adjusted by the movement of the tool.
OSG's ThreadPro program creation app for thread mills automatically performs time-consuming calculation work by inputting the processing details of the screw, and then creates a machining program from the numbers. It is possible to significantly reduce the preparation time for threading in a thread mill.
5.3 Tool wear requires readjustment of tool diameter compensation
Since the thread mill wears out and the tool diameter decreases as it continues to be processed, when machining with the same trajectory, the finish tends to be smaller in the case of internal threads and the finish in the case of internal threads tends to be larger. Therefore, in order to adjust the amount of regular wear, it is necessary to adjust the tool diameter correction value each time. In addition, even if the solid type is re-polished, it is necessary to adjust the tool diameter correction value again to pass the gauge after re-polishing.
In order to quickly respond to the correction work of tool diameter correction, we recommend the diameter correction tool DCT for thread mills. The DCT can easily measure the effective diameter of the mouth of a screw machined by a thread mill, and anyone can easily and quickly adjust how much tool diameter correction is required until the gauge is passed.
・Diameter correction tool for thread mills_DCT
6: FAQs
6.1 Conventional JIS2 grade thread processing
6.2 I want to pass with a screw gauge. What is the procedure for adjusting the tool diameter correction value?
6.3 Threading of high-hardness steel of about 60HRC
6.4 Oversize threading
6.5 Tapered threads shorter than short threads
6.6 Machining Insert Threads
6.7 I want to make sure that I don't hit the bottom of the pilot hole.
6.8 Machining the Left Thread
(FAQID:14694)