エンドミルやインデキサブル( チップ交換式)カッタで、ヘリカル加工を行う時の切削条件はどのように計算すればよいかをご紹介します。
例として、超硬防振型エンドミルAE-VMSS φ10でφ18の穴をランピング角度3°でヘリカル加工する場合で考えてみましょう。
カタログの推奨条件は、回転速度3,200min-1、送り速度840mm/minです。
①カタログ掲載の溝加工推奨条件から目安を計算
回転速度と1回転あたりの送り量は、カタログ推奨条件の溝加工条件から×70%を目安にします。
回転速度(目安)=3,200×0.7=2,240min-1
1回転あたりの送り量(目安)=(840÷3,200)×0.7=0.18375mm/rev
②加工径と工具径から、送り速度の補正
機械の送り速度「F」は「工具中心の移動速度」です。
一方向への工具移動であれば、「工具中心の移動距離」と「工具外周の移動距離」は同じになります。
カタログ条件表の数値はこちらの考え方で表されています。
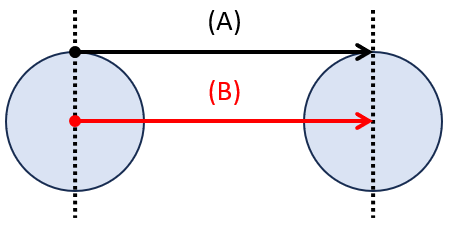
【一方向へ移動の場合】 (A)工具外周の移動距離 (B)工具中心の移動距離
しかし、円弧加工の場合、工具中心と工具外周の移動距離は異なります。
ということは工具が1周するときの工具中心と工具外周の移動速度も異なります。
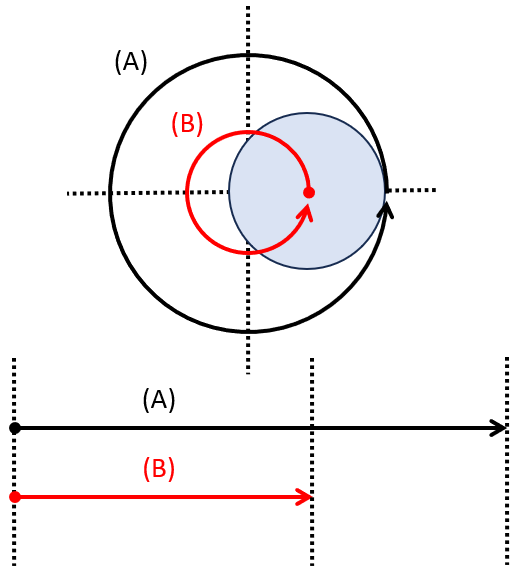
【円弧移動の場合】 (A)工具外周の移動距離 (B)工具中心の移動距離
仮に、送り速度の指令値を一方向の場合にして円弧切削を行おうとすると、実際の工具外周の送りは指令値よりも高くなってしまい工具破損のリスクが高くなってしまいます。
そのため、工具中心の動きであるプログラム上の「F」を補正し、工具外周が加工に適した送り速度で移動できるようにします。
まず、工具外周の移動量(=加工径)と工具中心の移動量に対する割合を計算します。
超硬防振型エンドミルAE-VMSS φ10でφ18の穴をヘリカル加工する場合
(加工径-工具径)÷加工径=(18-10)÷18=0.444・・・
①で求めた回転速度(2,240min-1)と1回転あたりの送り量(0.18375mm/rev)にこれを掛けます。
2,240×0.18375×0.4444・・・≒183mm/min
この数値が補正後の送り速度となります。
③ヘリカル1周当たりにZ軸方向に移動する距離の計算
ヘリカル加工では、円弧補間の動きとZ軸方向の動きの指令が同時に働きます。
工具中心の移動する距離(径方向のみ)に対し、どれくらいの傾斜(ランピング角度)で下がっていくかを計算をします。
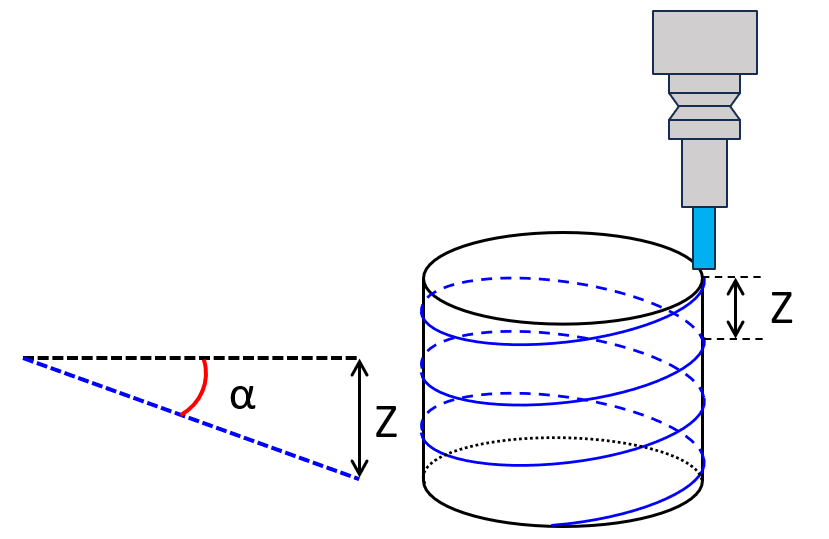
(α)ランピング角度 (z)Z軸方向の移動距離
工具中心の移動する距離(径方向のみ)を「X」とすると
X=(加工したい穴径-工具径)×3.14
AE-VMSS φ10でφ18の穴をヘリカル加工する場合
X=(18-10)×3.14=25.12(mm)
工具が軸方向に移動する距離を「Z」とすると
Z=X×tan(ランピング角度)
一般的なランピング角度は2~3°が目安となります。
Z=X×tan3°=25.12(mm)×0.05240=1.316(mm)
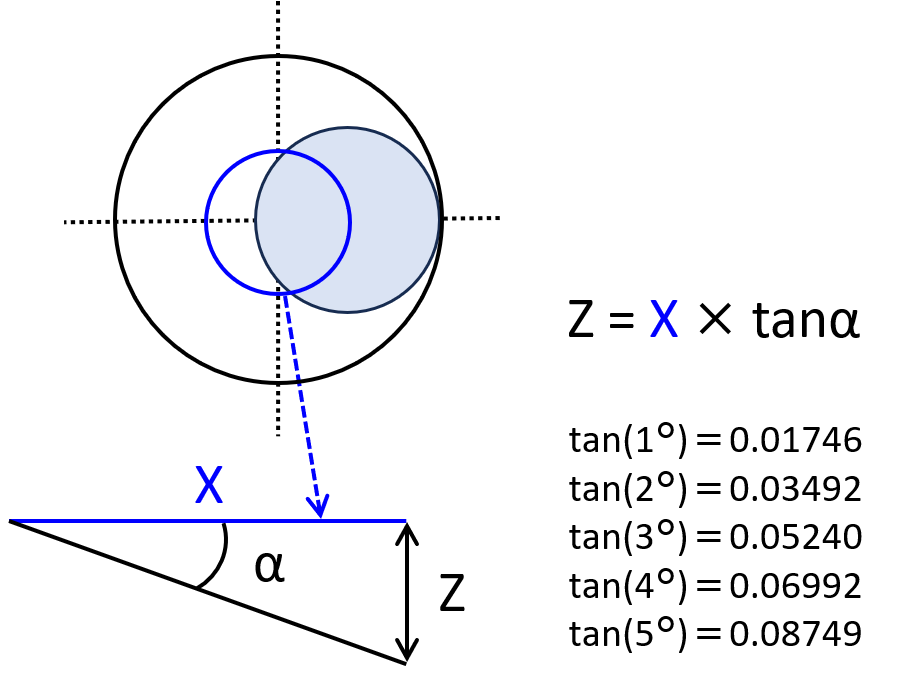
(α)ランピング角度 (X)工具中心の移動する距離(径方向のみ) (z)Z軸方向の移動距離
ここでのタンジェントの値は、底辺を1とした際の各角度における高さの割合です。
工具中心(径方向のみ)(mm)に、その角度のタンジェントの値をかけることで高さ(mm)を算出できます。
以上で、ヘリカルの動きに必要な回転速度(S)、送り速度(F)、ヘリカル1周当たりにZ軸方向に移動する距離(Z)の数字を算出することができました。
実際の加工においては、工具や被削材の振れ、切りくず排出などを考慮した調整を行ってください。